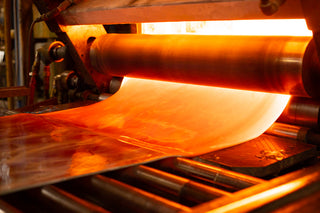
oceanside compatible®
The Continuous Ribbon Process
Unique in the art glass world
During the 1920's, one of the most important technological advances in the history of sheet glass took place: the development of a production process called the "Continuous Ribbon." This new system took four separate phases of sheet glass production (raw material introduction, melting, sheet forming, and annealing) and combined them into one continuous operation, making possible the production of large quantities of glass with very uniform and stable properties. Volume was boosted, costs were lowered, quality was improved, and the Continuous Ribbon became the heart of modern plate glass production.
Fifty years later, in 1976, the Continuous Ribbon process was successfully adapted for art glass production. Three Seattle glass lovers with backgrounds in engineering noticed the increasing and unsatisfied demand for art glass. They gambled that it was technologically possible and economically feasible to create multi-colored glass in a Continuous Ribbon system, integrating old-world methods with modern glass technology. Their success was the beginning of Spectrum® Glass Company, and the process they pioneered is now owned and utilized by Oceanside Glass and Tile®.

Glass moves from the hot end to the cold end in one continuous ribbon.
In the Continuous Ribbon process, raw materials are introduced into a large tank furnace, displacing existing molten glass and forcing it, stream-like, down a channel into the stirring bay. From there, the glass flows through a pair of water-cooled forming rolls, flattening into uniform thickness and becoming an endless ribbon of sheet glass. The ribbon passes through a long tunnel of individual oven sections, which gradually anneal and cool the glass until finally, at the “cold end” of the production, the long ribbon is cut into sheets and placed in crates.
To create multi-colored glasses, the desired secondary glass colors are melted in separate smaller furnaces. The additional molten glass is then ladled into the base stream just ahead of the stirring bay, where the different glasses are carefully stirred together by a skilled operator using a hand-held rod. Of course, both the timing of the ladling and the stirring technique are critical to the end result, and vary for different products. Our popular "Wispies" are made by ladling small amounts of white opal into the flow of a transparent color base. The more opaque varieties are just the opposite—small amounts of transparent color are ladled into a flow of opal glass. To get just the right mix, ladlers pour at carefully timed intervals, watching clocks equipped with timing lights to cue their movements.

Stirring technique is also very important. Inadequate stirring results in uneven distribution of color across the sheet. Over-stirring causes a muddy appearance and destroys definition between the colors. If the glasses are stirred too little, they tend to repel each other, creating splotchy areas and wide gaps in the mix. And to make things even more challenging, products like Baroque™ and OpalArt™ require a completely different stirring technique to create and sustain their unique characteristics. These skills can, literally, take years to master.
Our innovative Continuous Ribbon process allows us to create the smoothest, most consistent art glass sheets on the market. It was patented way back in 1979, and it remains the only one of its type anywhere in the world.
Oceanside Glass & Tile®