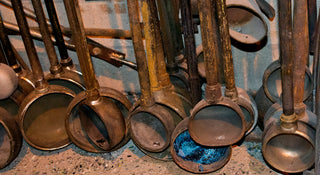
FAQ
Frequently Asked Questions
General Questions
Below are some common questions we hear from our customers
We hope to offer guided tours in the future, but unfortunately, at this time we aren’t set up for it. Be sure to sign-up for our emails to receive any notifications on this topic. In the meantime, there are videos throughout the site that show our processes in good detail.
We have obtained permission from the artists whose work appears on our website to use the images. as we have. You need to do so also. Please contact the artist/studio that produced the work.
There are a number of terms you may bump into from time to time that leave you scratching your head. We have a glossary of glass terms that just might answer some of your questions.
Purchasing Questions
Below are some common questions we hear from our customers
At this time, we do sell some products online and we may choose to expand that in the future. Historically however, a distribution chain has served us well and is in place for the majority of our products. Our continuous ribbon process allows us to produce large volumes of sheet glass that are packed into full cases per color. Because full cases of 48” x 24” sheets are not easily consumed, we have utilized a tiered distribution system to buy cases in bulk, break down that bulk, and move it to retailers who take the same process a step further.
At this time, Color Bar, Sample Sets, and Merch can be purchased online.
For all other products, please visit our dealer locator to find where you can purchase our products.
Individual sample pieces are generally available through your supplier. For requests from interior design or architectural firms, please send us an email and we will assist you in locating samples of the products you are looking to view in person, or source.
Products
Below are some of are common questions about our products
Good question! It’s a bit of a long-winded answer, but many find it very useful to understand, so we invite you to read all about it here: Understanding Our Numbering Systems.
There are any number of reasons why we choose to discontinue a product. It is never a simple decision, and it's always more complex than just "slow sales.” There's usually a compounding production-related factor, such as raw material sourcing issues, or equipment/scheduling limitations, combined with poor demand for the product, that ultimately lead us to choose to discontinue a product.
Certainly. There have been many cases of products being reinstated to the standard line. It usually means we've solved the production issues that originally led to its demise and feel demand is strong enough to warrant making it again.
Normally it's due to our inability to accurately predict the future. The nature of our Continuous Ribbon sheet glass process requires us to run an extended color cycle. That is, the colors must be run in a set sequence, and it takes months to go through the cycle. So, when we make red, for example, we make enough to stock and sell for the entire length of the color cycle—until we get back to red production again. Sounds simple enough, but the longer the cycle, the harder it is to accurately predict sales volumes.
At other times, our capacities have been so overburdened that we've chosen to skip certain products in the cycle in favor of others. Knowing that we're going to be out of something, we might to choose to produce Clear Waterglass® sheets but skip Orange as the Clear is in much higher demand. These are tough decisions but, fortunately, they are rare.
Raw material costs and sourcing can also affect the production choices we make.
Oceanside Compatible™ “Fusible Range” (FR) glass is tested Oceanside Compatible, yet falls outside of a stock item’s standard visual characteristics in some way (color, translucency, surface, mix, etc.). These quality fusible sheets offer excellent savings for Fusers whose creations do not require strict color tolerances for their work. Check with your Supplier for availability of 80-Sheet Rack Pack boxes of FR glass.
Absolutely. In some products it's obvious, in others, less so. Generally speaking, the shinier side is the top or front side of the sheet. Rolled textures are always textured on the back side of the sheet.
We call them "seed tracks." In some particularly gaseous glass compositions, a bubble will form in the stirring bay (the pool where glasses of different colors are stirred together). That bubble pops as it's drawn through the sheet-forming rolls, creating a "track" on the sheet surface. We make every effort to keep them to a minimum.
In glasses that aren't intentionally seedy, the seed count and size vary with the nature of the glass composition. Some glasses, notably ambers, champagnes and purples, are naturally more gaseous in nature than others. Gas in the glass equals bubbles in the sheet.
Sure, but it might break in the process. Tempering is performed by glass fabricators to allow glass to shatter safely into small pebble-like pieces. Essentially, it is a process of putting the stress that we've so carefully annealed out of the glass, back into it. Successful tempering depends on the particular glass's ability to stand up to induced internal stresses. So, fairly simple glasses such as smooth cathedrals will temper fairly well and more complex ones, such as a Baroque, may be less cooperative.
Look for a fabricator who is willing to test on a small scale and experiment with the tempering process to find a set of time-temperature relationships that will provide acceptable results. Acceptable results would be a rate of loss (breakage) in the tempering process that your fabricator could live with. The trial & error process will require close cooperation of the tempering facility you're working with.
Bottom line: art glass of any kind will not temper as dependably as float glass because it's not made to be "perfect," or flawless as float glass is. But it can be done and has been. Consider lamination, when safety glass requirements need to be met.
Baroque is very unique. To make it, we mix together two or more glasses of intentionally mis-matched compositions. The glasses, of slightly different expansions, "resist" being mixed together and don't homogenize easily. Thus, the characteristic reamy pattern and high-contrast mixes. Due to the nature of Baroque, the sheets have slightly more internal stress than other Oceanside Glass & Tile products. Which means greater care is in order when cutting.
Baroque is a "reamy" glass, whose texture is produced by stirring together two glasses of carefully mismatched compositions. The glasses, of slightly different expansions, "resist" being mixed together and don't homogenize easily. Thus, the characteristic reamy pattern and high-contrast mixes. Due to the nature of Baroque, the sheets have slightly more internal stress than other Oceanside Glass & Tile products. Which means greater care is in order when cutting.
Baroque formulas call for two or more glasses of intentionally mis-matched compositions, of slightly different expansion rates. These mis-matched glasses (required to create the visual/textural effect of Baroque) so not hold up well in fusing processes.
It’s produced by over-stretching the glass ribbon as it emerges from the Forming Rolls, while it is still hot enough to shape. This stretching action forms the organically rippled Waterglass surface.
Score the glass on the back side (the flatter side) to ensure an even, uniform score. Don't forget to reverse your pattern if you want the wavy side out in the finished project.
The Waterglass® texture is created by stretching the molten glass ribbon as it exits the sheet-forming rolls. Grasp two ends of anything with some give and stretch it. Gets narrower, right? There 'ya go.
Different colors, even different densities of the same color, have different heat-retention properties, and thus, different viscosities at the same stage in the sheet-forming process. These properties directly affect the texture that results when the hot glass ribbon is "stretched." We do make adjustments during the runs for consistency of texture, but you will see some differences on close examination.
Compressed air is forced into the molten stream in the forehearth channel to create extra bubbles which form the “seeds” in Seedy glass.
Probably not, unless you require enough to purchase an entire day’s run, including any fall-down during production. Our final response depends entirely on what the request is, how much you need and your time frame. If you believe that your needs meet all of the above purchasing criteria, please send an email with specifics so that we may provide a complete answer
Immediately downstream from the sheet forming rolls, the hot glass is sprayed with a liquid metallic crystal that bonds to the surface, creating the colorful, shimmering reflections.
Oceanside Glass & Tile Ripple is another natural texture, as opposed to a rolled one. We operate the top and bottom forming rolls at different speeds, which sets up a 'jumping' tension between them, causing the dynamic ripple texture to form.
These are rolled textures. Their patterns are embossed on the bottom forming roll, which textures the sheet as it passes through.
No. Glue chip is a cold-glass process — a treatment done to glass sheets long after they're produced. Many glue-chip manufacturers do use Oceanside Glass & Tile glass, though. See the Glossary of Art Glass Terms for an explanation of how Glue Chip is made.
Color is created as part of the basic raw batching materials. Virtually any metallic oxide creates color in glass. Some of the most common include: cobalt (some Blues), copper (some Blues & Greens), manganese (Purples), sulfur (Ambers) selenium (Reds & Oranges), cadmium (Yellows), chrome (some Greens), fluorine (White opal) and nickel (Gray).
Not at this writing. Artique®, Rough Rolled, and Waterglass® have broad color selections but generally we limit the production of rolled textures (Hammered, Granite, etc.) to colors that sell well enough to justify carrying the inventory.
TROUBLESHOOTING QUESTIONS
Below are some common questions about troubleshooting issues.
Start by visiting our Tips & Tutorials section for materials designed to address the most common tech support questions received. Read through these first as you might find your answer is addressed in one of these documents.
Yes, we encourage our customers to review the tech support documents in the Tips and Tutorials section, but If you still have a technical product, or fusing question beyond that, please send an email to Artglass@Glasstile.com. Please remember to include as many details, photographs, production dates found on the sheet glass stickers, firing schedules, etc., as you can to help us understand the nature of your question and help us to more expediently assist you in finding answers to your issues.
Ah…trapped air bubbles. A common pet peeve and one that can fairly easily be avoided. Using a firing schedule with a bubble squeeze is often a great start toward trapping fewer bubbles. (See the Advanced 8-Segment Full Fuse Profile in our Firing Schedules.) Please also review our Tips and Tutorials section for troubleshooting and other useful information that can likely make things much easier for you, moving forward.
Small amounts of moisture in the kiln shelf or shelf primer may be turning to steam at high temperatures. Or, some organic material (dirt, metal filings or other debris) are burning and gassing off at fusing temperatures. The best way to prevent these types of gaseous bubbles is to use a Kiln Shelf Paper, such as Papyros, between the shelf and the glass. The paper is air-permeable and will allow more air to escape than a direct-shelf contact scenario.
For fusers who are certain they are using tested Oceanside Compatible products, this is most often traced back to a thermal shock issue related to using too aggressive of a firing schedule. We encourage everyone to review our suggested firing schedules. They are conservative (by design) and provide a safe jumping off point for most kinds of projects.
There is no one firing schedule that will accommodate all items fusers may make. Schedules should be adjusted to best suit a projects thickness, size and ultimate finished shape. We have a helpful document for those new to kiln forming who wish to better understand what’s going on during the various segments of a firing schedule — download here: Firing Schedule Dissected (PDF).
For kiln related questions – It is important to remember that all kilns fire slightly differently, and as kilns undergo repeated use, they can usually benefit from some TLC in the way of standard maintenance. The kiln manufacturers generally offer great resources to assist their customers with maintenance and repair issues.
More than likely, your firing temperature is too hot. Try experimenting with your fuse cycle. Either go to a higher temperature for a shorter amount of time or try a lower temperature for a longer period of time. Kiln Shelf Paper is a great alternative to primer and you won’t have to worry about it sticking to your piece.
Questions About compatibility
Below are some common questions about glass compatibility
Let the Oceanside Compatible logo be your guide to products that have been “Tested Compatible” within the Oceanside Compatible program. Please note that that products labeled as simply “COE 96” may not actually be compatible with true Oceanside Compatible products.
All of our Oceanside Compatible products are tested to ensure that they “compatibly fit” to work with each other during the kiln forming process. All accessories are also tested Oceanside Compatible. Oceanside Compatible products are additionally compatible with the original authentically branded “System96®” glass products.
All of our Oceanside Compatible products are tested to ensure that they “compatibly fit” to work with each other during the kiln forming process. All accessories are also tested Oceanside Compatible. Oceanside Compatible products are additionally compatible with the original authentically branded “System96®” glass products.
We do not test our product lines for compatibility against any other manufacturers’ “COE 96” labeled products, and therefore cannot speak to their compatibility claims. If you choose to mix manufacturers COE 96 products in your artwork, the onus is on you to test each project you make for incompatibility stress.
Really very little. What you learn with one glass will largely apply to the other. Oceanside Compatible is a lower temperature glass — that is, it takes less time / heat for Oceanside Compatible products to reach a given viscosity than it does common COE 90 products. Understanding this, and looking over the Oceanside Compatible Firing Guidelines, a kiln crafter will quickly adapt to the differences.
Didn't find your answer?
Don't hesitate to contact us